El objetivo de TSR Wind es optimizar y rentabilizar al máximo el mantenimiento de los aerogeneradores a través de la tecnología y la robótica, además de eliminar el riesgo de accidentes para los trabajadores inherente al sector eólico.
Una de las estrategias típicas durante la Operación y Mantenimiento de parques eólicos es la inspección manual de torres. Habitualmente, el operario sube a la torre para inspeccionar las soldaduras de la torre de acero descolgándose a través de cuerdas o con la ayuda de una plataforma elevadora. Este método implica una inspección manual, que supone varios días de trabajo para inspeccionar un aerogenerador completo, además del riesgo para el operario debido a la altura así como los elevados costes en el caso de utilizar plataformas elevadoras.
TSR Wind ha diseñado y desarrollado el Kratos, empleado para la inspección de soldaduras de las torres mediante ultrasonidos.
Kratos 200 tiene como objetivo ejecutar tareas de inspección de soldaduras mediante ensayos no destructivos (NDT – Non Destructive Technique) en torres de aerogeneradores. Esta plataforma robótica está diseñada para desplazarse sobre superficies de acero u otro material ferroso.
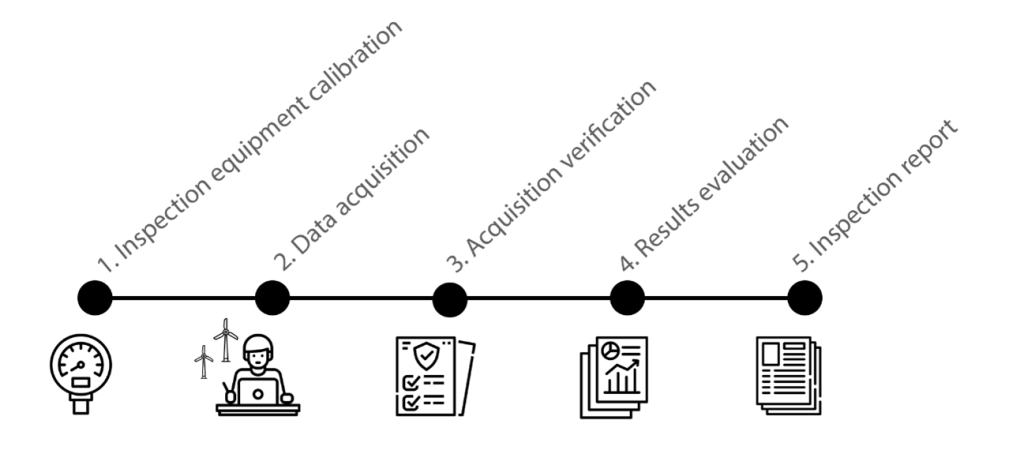
Ilustración 1. Procedimiento de inspección de soldadura realizado por un experto en ultrasonidos nivel II
La solución incluye varias innovaciones técnicas propias de gran complejidad:
- Sistema mecánico: que garantiza un movimiento omnidireccional preciso al tiempo que soporta la fuerza de atracción de los imanes y las perturbaciones causadas por la gravedad y el peso propio del robot y sus cargas útiles. Basándose en la misma familia de motores utilizada para otros robots de TSR, el equipo ha diseñado un sistema mecánico para acoplar un motor con su reductor directamente en la rueda, con un soporte mecánico que permite una rotación de 360 grados, aumentando la eficacia y reduciendo el peso del conjunto completo en comparación con el primer prototipo.
- Soporte de sonda ad-hoc: capaz de presionar la superficie de la torre, adaptándose a diferentes diámetros, geometrías de soldadura, proyecciones e impurezas, al tiempo que se desplaza con una precisión milimétrica.
- Sistema de control: diseñado especialmente para actuar sobre la inclinación y altitud del robot mientras se desplaza siguiendo la soldadura en una inspección, evitando la deriva gravitatoria mientras se desplaza horizontalmente.
Los potentes imanes de neodimio le permiten subir a una torre de hasta 100 metros de altura a una velocidad de 5 metros por minuto.
Ilustración 2. Kratos 200
Aunque el robot está preparado para trabajar de forma autónoma, un operario revisa el proceso de inspección observando su ubicación con un dispositivo conectado mediante fibra óptica para proporcionar una conexión de alta velocidad entre el robot y la estación de operaciones.
Las soldaduras se inspeccionan acoplando al robot un dispositivo inteligente portasondas equipado con palpadores motorizados que se pueden controlar de forma independiente. La presión de acople es ajustable según la superficie y está dotado de un sistema de detección de soldaduras basado en visión por ordenador que guía de forma automática al robot durante el proceso. Para la correcta inspección y detección de fallos en las soldaduras se utilizan dos métodos de ensayo por ultrasonido, Time of Flight Diffraction Technique (ToFD) y Phased Array (PAUT).
Ilustración 3. Ejemplo de daño. Materiales analizados por ultrasonidos
En lugar de otros materiales acoplantes, se utiliza una pequeña cantidad de agua que el robot dispensa en cada uno de los palpadores y se utiliza tanto en el proceso de calibración como en la adquisición de datos.
La información del Kratos puede ser recogida y revisada en tiempo real por un experto en ultrasonidos o descargada para una inspección posterior.
Además de recoger datos de ultrasonidos, Kratos utiliza cámaras de vídeo de alta calidad para grabar todo el proceso, así como evaluar en tiempo real cualquier otro defecto visual de la torre y evaluar si necesita algún tipo de mantenimiento.
La duración de la inspección es dependiente de la altura del aerogenerador y del número de soldaduras a inspeccionar, pudiendo llegar a un día para cubrir todas las soldaduras de la torre de un aerogenerador.
El experto en ultrasonidos analiza los resultados obtenidos durante la toma de datos y elabora un informe que se incorporará a la plataforma TSR Inspector. En esta aplicación de desarrollo propio, el cliente puede ver los resultados en cualquier dispositivo con conexión a internet y descargar cómodamente los informes para consultarlos en cualquier momento.
Kratos 150 se ha sido utilizado en la inspección de más de 200 soldaduras durante la primera fase del proyecto.
Inspección ultrasónica para prolongar la vida útil
Como se ha mencionado anteriormente, la torre del aerogenerador es un componente clave del sistema, por lo tanto, las inspecciones de las soldaduras de la torre están altamente relacionadas con la extensión de la vida útil de la turbina. El estado de las soldaduras afecta directamente a la integridad de la torre y mantener inspecciones periódicas es una forma de asegurarse de que no hay daños en la estructura. Algunos ejemplos de daños graves que Kratos puede detectar en las soldaduras son grietas, fisuras y defectos de fabricación con profundidades superiores a 2 mm. Está claro que el tiempo puede alargar estos daños hasta que se conviertan en un gran problema para las torres.
Además, el robot también es capaz de detectar defectos más pequeños, como poros o falta de fusión, antes de que se conviertan en algo peor.
Tener todas las inspecciones guardadas en TSR Inspector aporta al cliente la posibilidad de disponer de toda esta información útil en una sola plataforma. El almacenamiento de estos datos supone la creación de una importante base de datos que el cliente puede consultar en cualquier momento y observar la evolución de los daños a lo largo del tiempo.
Ahorro para propietarios y O&M
Utilizando este método de inspección robotizada, el propietario del parque eólico puede optimizar y reducir el presupuesto de inspección de soldaduras de las turbinas en un 50% como mínimo. Además, el tiempo de inspección se reduciría en un tercio, lo que significa menor tiempo de inspección, mayor producción y tiempo de uso de la turbina.
Otra característica clave del uso de robots TSR es que, si las normas de seguridad del parque lo permiten, el robot puede inspeccionar la torre de la turbina mientras está en funcionamiento. Esto significa que durante el periodo de inspección la turbina puede seguir produciendo energía para evitar la pérdida de ingresos.
Un robot con muchas posibilidades
El Kratos ofrece muchas posibilidades a los operadores de parques eólicos. Su sistema de sondas, donde se realiza la monitorización por ultrasonidos, es sólo una de las funcionalidades de Kratos. También es capaz de levantar cargas pesadas y desplazarse en cualquier dirección por la torre. Este robot podría ayudar a los técnicos de mantenimiento que trabajan en altura a levantar ciertas herramientas pesadas, acoplar otro tipo de sistema de ultrasonidos, realizar trabajos de decapado, repintar el aerogenerador, realizar ensayos no destructivos, instalar sensores o antenas, y muchas otras funcionalidades complementarias.
Aparte de la industria eólica, nuestra visión en TSR Wind está ampliamente abierta a aplicar nuestras soluciones en otros sectores industriales. Aunque hemos inspeccionado más de 4400 turbinas, las soluciones de TSR Wind han sido examinadas en algunos tanques de almacenamiento industrial proporcionando excelentes resultados. Normalmente, este tipo de inspecciones se realizan montando grandes andamios, sin embargo, Kratos proporciona una solución de inspección óptima para cualquier estructura con superficies de acero u otros materiales ferrosos.
En definitiva, el robot Kratos está listo para cubrir la gran demanda y servicios que existe en todo el mundo. La complejidad y multifuncionalidad de Kratos lo convierten en una solución única para un proceso fiable de inspección de soldaduras mediante tecnología de ultrasonidos. Kratos se considera una solución fundamental para los procesos de prolongación de la vida útil de los parques eólicos.